The aerospace and defence (A&D) industry is no stranger to labour shortages. With a reliance on highly skilled, well-paid professionals, it’s an industry that’s historically experienced difficulties in hiring and retaining the right people across the supply chain.
Often, these labour shortages are short-lived. When OEMs are forced to lay off staff temporarily due to financial struggles, they’re frequently hired back within a few months. Even in the worst-case scenarios, such as the 2008 financial crash, professionals returned to the industry. But following the COVID-19 pandemic, OEMs in the A&D industry face a very different situation.
After the pandemic, the A&D industry recovered slower than many other manufacturing-led industries – and a lot of the professionals who lost their positions in A&D moved to other industries.
Now, A&D is experiencing a wide-scale labour shortage that’s likely to last for multiple years. And that’s just one part of the challenge OEMs are facing.
Supply chain disruption paired with growing demand
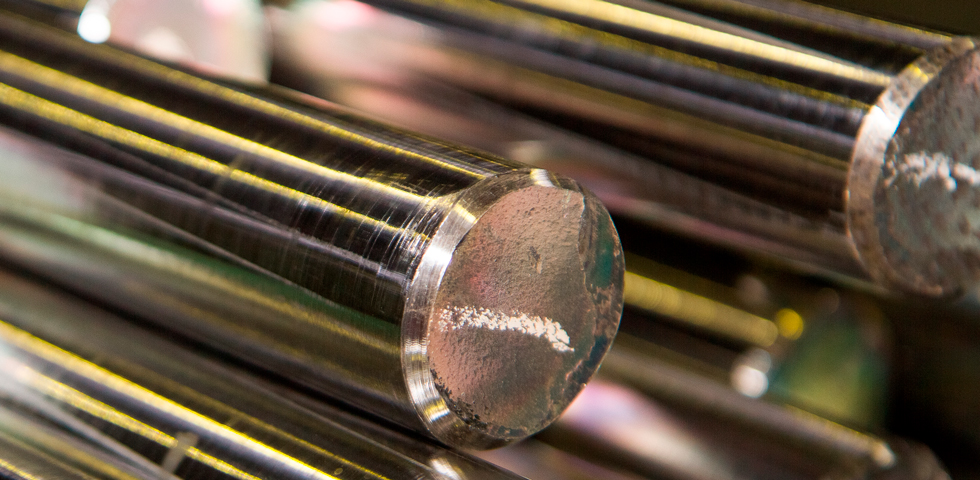
Combined with the labour shortage is a materials shortage across key materials such as titanium, due to the effects of the Russia-Ukraine war. Russia is one of the world’s leading players in the titanium and titanium forging markets, and the conflict has significantly restricted many suppliers’ access to the metal.
Like many material shortages, this isn’t expected to be a long-term challenge. However, in the short term, limited access to titanium is considerably slowing many OEMs’ production schedules.
The materials and labour shortages have also come at a time when demand for aircraft production is rapidly rising. In aerospace, the demand for commercial flights is growing above pre-pandemic levels. But with more eco-conscious consumers and new sustainability targets, many organisations are looking to phase out wide-body aircrafts to make room for more fuel- and emission-efficient models, raising the pressure on OEMs to rise to this demand.
At the same time, many countries are raising their defence budgets, with a significant portion being allocated to air defence capabilities – ultimately creating additional demand that OEMs need to meet.
Growing challenges with limited solutions
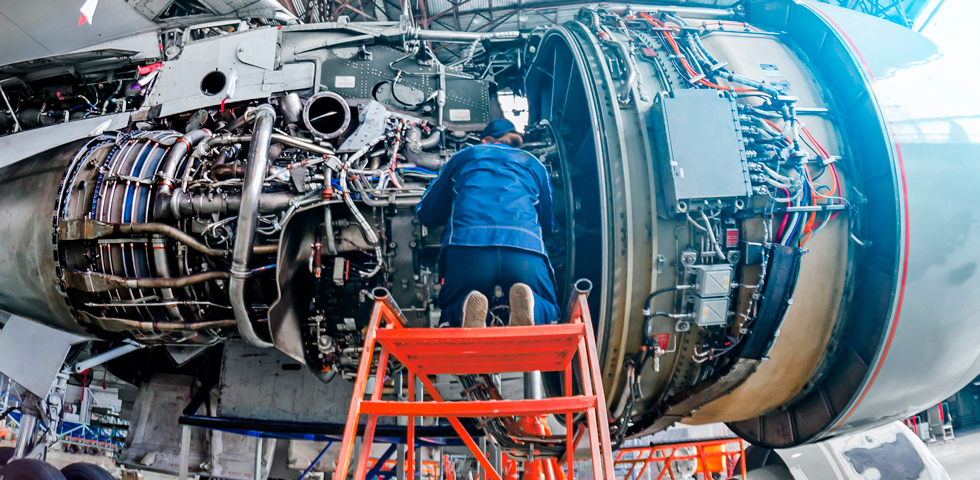
All these challenges leave OEMs in a difficult position, with seemingly few solutions.
Many are currently trying to address the labour shortage challenge by hiring new talent, but a large proportion of the professionals entering the market don’t have the experience needed to drive a lot of OEMs’ projects. In some cases, OEMs are even considering where parts of the supply chain can be automated – but this isn’t going to happen overnight, and can’t provide an immediate solution to the challenge.
For their materials challenges, some OEMs are attempting to partner with new suppliers who have access to materials such as titanium. Many companies have contracted Japan-based firms as alternatives to Russian suppliers, but in a lot of cases, it’s taking as long as three to four months to get the necessary approvals to commence supply.
Four areas to focus on amid supply chain disruption
To successfully tackle their supply chain challenges – and prevent financial instability – OEMs will need to look more closely at their tier one and tier two suppliers and identify potential risks and opportunities across them. They need to monitor risks for critical parts and materials to gauge interdependence with other end-use industries; the impact of geopolitical and other macro events; and cost and sourcing challenges to develop long-term strategies to ensure a world-class supply base.
Here are four areas where we recommend you should start focusing on:
- Develop a more resilient supply chain
The last few years have been highly turbulent for the A&D supply chain due to several disruptions, including the COVID-19 pandemic, shipping container shortages and most recently, the Russia-Ukraine war. Strategies such as single sourcing and low-cost sourcing have proved to be highly risky due to limited knowledge about the suppliers’ stability and performance.
With more frequently generated insights, supplier risk monitoring will give a better chance of spotting adverse developments or negative patterns among your suppliers and pre-empt risks. For example, this could be recognising a materials shortage trend among suppliers in a specific continent or spotting a labour strike trend before it affects production schedules.
- Gauge inherent category risks
Supply chains have become ever more intertwined and complex over the last two decades as category teams continuously strive to reduce costs and achieve savings, riding on continuing globalisation and improving global trade conditions. This resulted in a few suppliers dominating the supply of materials/products for certain categories, such as semiconductors, high-value alloys and complex fabrications.
Hence, it is critical for organisations to assess risk and criticality of sub-tier suppliers and gain visibility across the supply chain. Additionally, the evolution of supply landscapes for critical components and materials will help category teams develop the supply chain for the future as A&D companies look to achieve net-zero emissions by 2050.
- Prepare for geopolitical and regulatory interventions
Due to increasing trade imbalance, people unrest and high debt and unemployment level, governments across the world are resorting to trade interventions and inward-looking policies to protect their interests. As a consequence, sourcing strategies and supply chains need to be developed keeping in mind the evolving geopolitical agenda and changing regulations that will reshape supply chains in future.
Whether we talk about the US-China Trade War, the US and EU chips act to create domestic semiconductor capacity or Germany’s Supply Chain Due Diligence Act, which will require companies to monitor their supply chains for human rights and environmental standards compliance – A&D companies will need to redraw their supply base.
- Partnership with suppliers
An accurate view of your suppliers’ capabilities, customers and financial stability will help you identify those who might need temporary support from your organisation to continue operating at the level you need them to, which will enhance supplier relationships.
This could mean engaging with your suppliers to offer financial support to help them address their labour shortages and get their production schedules back on track. Or, in some cases, it could mean transferring some of your workforce to their sites to lead production on certain projects.
How The Smart Cube can help
Gathering all these insights on your suppliers while you’re trying to tackle other pressing challenges in your organisation can be difficult.
At The Smart Cube, our supply chain and risk experts help A&D organisations worldwide generate this intelligence across their supplier base daily. Our team can help you identify potential supply risks as soon as they emerge, examine your risks in detail, and offer clear next steps to mitigate any disruption.
To find out more about our category, commodity, and supplier risk solutions, and discover how they can help your teams thrive amid labour and material shortages, visit our website.